Any job, big or small! We have the team of professionals to get the job done right and exactly when you need it.
Let us quote your fabricating requirements today!
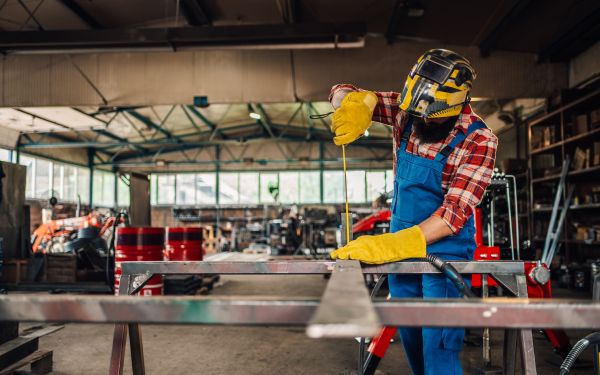
Steps in Metal Fabrication
Design: The process begins with conceptualizing the design of the metal structure or part based on the client’s specifications and requirements.
Material Selection: Choosing the appropriate type and grade of metal is crucial for the project’s success. Factors such as strength, corrosion resistance, and cost are considered during material selection.
Fabrication: This stage encompasses cutting, forming/bending, welding, and machining processes. Metal sheets or plates are cut into the required shapes and sizes using tools like laser cutters, water jets, or plasma cutters.
Assembly: Once all the metal components are prepared, they are assembled together using techniques such as bolting, riveting, welding, or adhesives to create the final product.
Finishing: The fabricated metal structure undergoes surface finishing processes like painting, powder coating, or galvanizing to enhance its aesthetics and improve durability.
Quality Control: Throughout the fabrication process, quality checks are conducted to ensure that the final product meets the required specifications and standards.
Delivery and Installation: The final step involves delivering the fabricated metal product to the customer and, if necessary, installing it. Proper packaging and transportation are essential to prevent damage during transit. Installation may require additional assembly and fitting on-site.
Main Processes in Metal Fabrication
Cutting:
-
Shearing: This involves cutting straight lines through metal sheets using a blade.
-
Laser Cutting: A highly precise technique that uses a laser to cut intricate designs.
-
Plasma Cutting: Utilizes a plasma torch to cut through thick metal with high precision.
-
Waterjet Cutting: Employs high-pressure water mixed with abrasive materials to cut metal without generating heat, which is ideal for heat-sensitive materials.
-
Bending:
-
Press Brake Bending: Utilizes a press brake machine to bend metal sheets by pressing them into a die.
-
Roll Bending: Involves passing metal through rollers to achieve a desired curve or cylindrical shape.
-
Machining:
-
Milling: Removes material using rotary cutters to shape the metal.
-
Turning: Spins the metal workpiece on a lathe while a cutting tool shapes it.
-
Drilling: Uses a rotary cutting tool to create holes in the metal.
-
Joining:
-
Welding: Common methods include MIG (Metal Inert Gas), TIG (Tungsten Inert Gas), and SMAW (Shielded Metal Arc Welding). Welding joins metal parts using heat or pressure.
-
Brazing and Soldering: Use filler metals to join parts without melting the base materials, ideal for delicate or heat-sensitive components.
-
Finishing:
-
Grinding and Polishing: Enhance the surface finish and remove any imperfections.
-
Coating: Includes processes like powder coating, painting, or anodizing to protect the metal and improve its appearance.
-
Galvanizing: Coating metal with zinc to prevent corrosion.
-
Forming:
-
Forging: Involves shaping metal using compressive force, typically with a hammer or die. Forging can be done at various temperatures, including cold, warm, and hot forging.
-
Casting: Molten metal is poured into a mold and allowed to solidify into the desired shape. This process is efficient for producing large quantities of identical parts.
-
Extrusion: Pushes metal through a die to create long shapes with a consistent cross-section, such as tubes and rods.
-
Stamping:
-
Uses a stamping press to create shapes, letters, or images on the metal surface. This process is often used for mass production of parts like coins and electronic components.
-
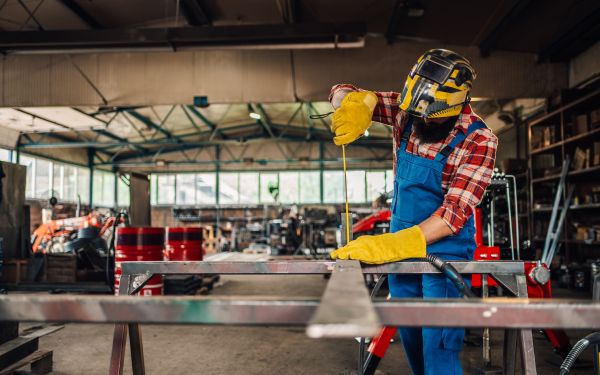